Черновое обтачивание цилиндрических поверхностей. Резцы для чернового обтачивания.
Закрепление детали при черновом обтачивании. Способ закрепления детали при черновой обработке выбирается в зависимости от ее формы, размеров, назначения и т. д. по правилам, изложенным в гл. III первой части книги. Следует помнить, что при черновом обтачивании деталей снимаются стружки больших сечений, вследствие чего возникают значительные силы резания, под действием которых деталь может быть вырвана из патрона. Поэтому закрепление детали в рассматриваемом случае должно быть особенно прочным.
Резцы для чернового обтачивания. Резцы для чернового обтачивания работают обычно при большом сечении стружки и часто при высокой скорости резания. Поэтому такой резец должен быть прочным, хорошо поглощать теплоту, образующуюся в процессе резания, и не терять твердости от нагревания во время работы. Форма передней поверхности резца должна быть такой, чтобы отделение стружки происходило с возможно большей легкостью.
Твердосплавные резцы для чернового обтачивания, называемые проходными, изображены на рис. 77. Прямые проходные резцы (рис. 77, а и б, отличающиеся друг от друга лишь формой твердосплавной пластинки) изготовляются с главным углом в плане угол = 45, 60 и 75°. Отогнутые проходные резцы (рис. 77, в), обычно штампованные, сложнее в изготовлении. Тем не менее они широко применяются, так как ими можно производить не только продольное, но и поперечное обтачивание (подрезание). Кроме того, они иногда удобнее при обработке поверхностей, трудно доступных для прямого резца. Главный угол в плане у этих резцов равен 45°.
Проходные упорные резцы (рис. 78) особенно пригодны для обработки детали с уступами небольших размеров, образуемыми этим же резцом. Главный угол в плане этих резцов 90°, что способствует уменьшению вибраций в процессе работы. Поэтому упорные резцы успешно используются при обработке нежестких деталей.
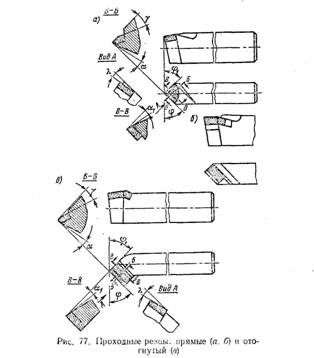
Быстрорежущие резцы по своей форме подобны твердосплавным резцам того же назначения, но отличаются от них, как это будет показано ниже, величинами углов и другими элементами головки.
Правые и левые резцы. По направлению подачи, при которой работают проходные резцы, они разделяются на правые и левые. Правыми резцами называются такие, у которых при наложении сверху ладони правой руки так, чтобы пальцы были направлены к вершине резца, главная режущая кромка оказывается расположенной со стороны большого пальца (рис 79, б ). На токарных станка х эти резцы работают при подаче справа налево, т. е. от задней бабки к передней. Левыми резцами называются такие, у которых при указанном выше наложении левой руки главная режущая кромка расположена также со стороны большого пальца (рис. 79, а ).
Материалы, применяемые для проходных резцов. Проходные резцы, используемые при обработке стальных и чугунных деталей, изготовляются с пластинками из твердых сплавов и из быстрорежущей стали. Марки твердых сплавов, используемых для обработки стали и чугуна при различных условиях резания, указаны в табл. 9.
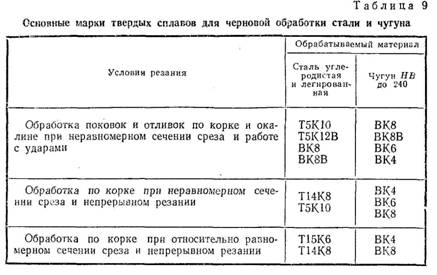
С меньшей, иногда значительно, производительностью обработку стали и чугуна при условиях, указанных в таблице, можно выполнять резцами из быстрорежущей стали марки Р18 (или других марок).
Элементы головки и углы твердосплавных резцов. Форма передней поверхности твердосплавных резцов устанавливается в зависимости от обрабатываемого материала, характера обработки, подачи и некоторых других условий.
Формы передней поверхности у резцов с пластинками из твердых сплавов приведены в табл. 10.
Передняя поверхность формы I рекомендуется для резцов при обработке серого чугуна, бронзы и других хрупких материалов, а также при тонком и чистовом точении с подачами s < 0,2 мм/об. Форма II передней поверхности используется при обработке ковкого чугуна, стали и стального литья с с б в 80 кгс/мм2, а также и с б в > 80 кгс/мм2 при недостаточной жесткости системы СПИД. Форма III делается у резцов, предназначенных для обработки стали с б в 80 кгс/мм2 при необходимости завивания и дробления стружки. Форма IV применяется при черновой обработке стали и стального литья с б в > 80 кгс/мм2 с неметаллическими включениями, при работе с ударами в условиях жесткой системы СПИД. Форма V рекомендуется при обработке нержавеющих сталей с б в 80 кгс/мм2.
Значения переднего угла твердосплавных резцов выбираются в зависимости от обрабатываемого материала; они указаны в табл. 11.
Задний угол а у твердосплавных резцов, используемых для черновой обработки стали и чугуна, делается равным8°.
Главный угол в плане ф твердосплавных резцов, применяемых в условиях нежесткой системы СПИД, принимается равным 90°. Если обработка происходит при большей жесткости этой системы, главный угол в плане может быть 60 — 75°. При значительной жесткости системы СПИД главный угол в плане принимают равным 45°.
Вспомогательный угол в плане ф 1 при черновой обработке принимается равным 5—20°, а иногда и больше.
Угол наклона главной режущей кромки Я при обработке резцом с ф = 90° принимается равным 0°. При главном угле в плане, меньшем 90°, этот угол делается для обработки стали 0—5°, а для чугуна 10°. При точении с ударами угол делают 12—15°.
Вершину резца закругляют радиусом 0,5—1,5 мм. Ширину фаски f принимают равной 0,15—0,5 мм. Меньшие значения принимаются при малом (12x12 мм и менее) сечении резца, большие — при резце сечения 25x25 мм и более.
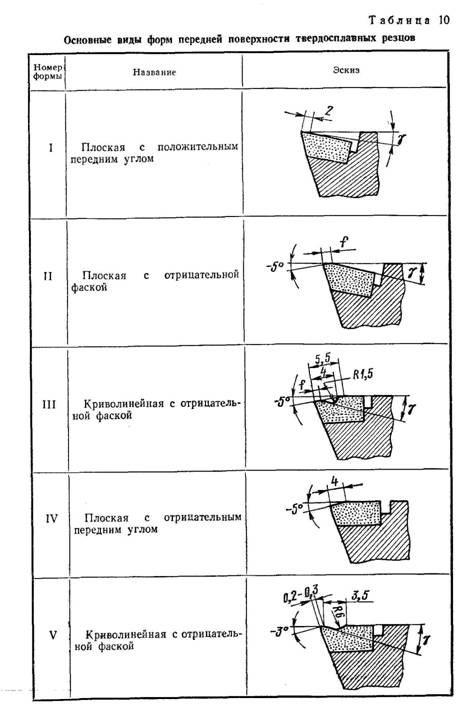
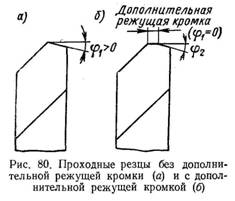
Проходные твердосплавные резцы для черновой и получистовой обработки выполняются как без дополнительной режущей кромки (рис. 80, а), так и с дополнительной режущей кромкой (рис. 80, б ). Как будет видно из дальнейшего изложения, резцы с дополнительной режущей кромкой позволяют вести обточку со значительно большими подачами, обеспечивая в то же время весьма хорошую шероховатость поверхности V4 — V51.
Форма передней поверхности, углы и другие элементы быстрорежущих резцов. Форма передней поверхности этих резцов выбирается в зависимости от обрабатываемого материала, подачи и некоторых других условий по табл.12 и в соответствии с общими соображениями, приведенными ниже.
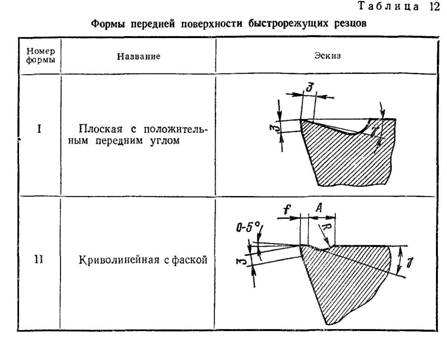
Передняя поверхность по форме I делается у резцов для обработки стали, а также чугуна, бронзы и других хрупких металлов. По форме II следует делать переднюю поверхность резцов для обработки стали с б в 80 кгс/мм2, вязких цветных металлов и легких сплавов при необходимости завивания стружки.
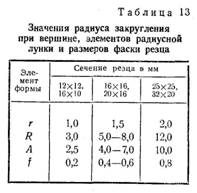
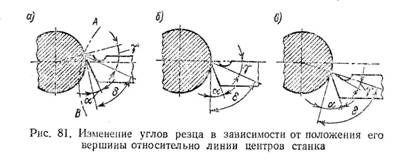
Передний угол рассматриваемых резцов, используемых для обработки стали, принимается равным 20—25°, а задний угол — равным 6°, при обработке медных сплавов передний угол — 20°, а задний — 8°. Значение главного и вспомогательного углов в плане, >а также угла наклона главной режущей кромки быстрорежущих резцов можно брать по соответственным данным для твердосплавных резцов.
Рекомендуемые значения радиуса закругления при вершине резца r элементов радиусной лунки R и А, а также размера фаски f в зависимости от сечений резца приведены в табл. 13. При обработке легких сплавов ширина фаски / принимается равной нулю.
Установка проходных резцов относительно линии центров станка. Условия работы резца изменяются в зависимости от положения его вершины относительно линии центров станка.
На рис. 81, б резец установлен таким образом, что вершина его находится на высоте центров станка. Задним углом его в этом случае является а, передним — у и углом резания — б.
При установке того же резца выше линии центров (рис. 81, а ) передний угол у увеличивается, а угол резания б уменьшается. Условия резания облегчаются, так как стружка легче сходит по передней поверхности, чем при меньшем переднем угле и, следовательно, большем угле резания. Одновременно с этим, однако, уменьшается задний угол а, что допустимо только до определенных пределов во избежание сильного трения задней поверхности резца об обрабатываемую поверхность (поверхность резания). Если этот же резец установить ниже линии центров станка (рис. 81, в ), то, наоборот, передний угол у уменьшается, а угол резания б увеличивается. В результате этого условия резания значительно ухудшаются по сравнению с первыми двумя случаями. Увеличение заднего угла а, получающееся при установке резца ниже центра, не улучшает процесса отделения стружки. Из сказанного вытекает общее правило, заключающееся в следующем.
При черновом обтачивании наружных поверхностей, когда наиболее легкое отделение стружки важнее всего, резец необходимо устанавливать или на высоте линии центров станка, или несколько выше ее, но не ниже.
От этого правила отступают при черновом обтачивании очень твердых материалов. В этом случае давление стружки на резец получается очень большим и резец отгибается вниз, причем вершина его (рис. 81, а) описывает дугу АВ. Если резец при этом установлен так, что вершина его расположена выше линии центров станка, он втягивается в материал детали. В результате этого неизбежны выкрашивание режущей кромки резца, а иногда и поломка его. При установке резца на высоте линии центров и в особенности ниже ее резец под давлением стружки также отгибается, но вершина его не втягивается в материал детали, а наоборот, отходит от нее.
Проверка положения вершины резца относительно линии центров станка производится по острому концу заднего центра или по риске, нанесенной на пиноли задней бабки.
Общие правила установки резца в резцедержателе. Чтобы резец во время работы не вибрировал, вследствие чего возможно выкрашивание его режущей кромки, длина свешивающейся части резца, или, как говорят, вылета, должна быть возможно меньше. На рис. 82, а показано правильное, а на рис. 82, б — неправильное положение резца.
С этой же целью подкладки под резец, применяемые при установке вершины резца относительно линии центров станка, следует располагать так, как показано на рис. 82, в. Неправильное положение подкладок показано на рис. 82, г. Лучше брать одну толстую подкладку, а не несколько тонких, так как они не всегда плотно прижимаются одна к другой (даже при затянутых болтах резцедержателя), что также может вызвать вибрацию резца.
Резец необходимо устанавливать под прямым углом к детали (рис. 82, д). Если установить резец по рис. 82, е, то во время работы под давлением снимаемой стружки он может повернуться вправо и углубиться в обрабатываемую деталь.
Некоторые особенности работы твердосплавными резцами с отрицательными передними углами. Работа резцами с отрицательными передними углами позволяет повысить режимы резания, но вызывает увеличенную нагрузку на механизмы станка и обрабатываемую деталь. Поэтому для обеспечения нормальной работы необходимо соблюдать следующие основные правила.
- Станок, на котором производится работа, должен быть в полном порядке. Подшипники должны быть нормально затянуты; ремень передачи и имеющийся на станке фрикцион должны быть хорошо пригнаны; суппорт станка должен двигаться плавно, без рывков.
- Деталь, обрабатываемая как в патроне, так и в центрах, должна быть закреплена надежно.
- Задний центр при работе на повышенных оборотах детали должен быть твердосплавным или вращающимся.
- При установке резца относительно центра станка при черновом обтачивании вершину его следует устанавливать выше центра на 0,01 диаметра обрабатываемой детали.
- Во избежание вибраций резца его вылет по величине не должен превышать высоты державки.
- Работать следует только доведенным резцом.
- Резец следует подводить к детали только при ее вращении. Врезание резца в деталь следует осуществлять вручную и постепенно, так, чтобы задняя вспомогательная поверхность не касалась обрабатываемой поверхности. Только после того, как врезание закончено, можно включить автоматическую подачу суппорта.
- Отводить резец следует до остановки станка, предварительно выключив автоматическую подачу.
- При точении по корке следует работать с наибольшей допустимой глубиной резания и избегать скольжения резца по окалине.
- Ширина среза не должна превышать 2/3 длины режущей кромки резца.
Режимы резания при черновом обтачивании твердосплавными резцами. Глубина резания при черновом обтачивании обычно бывает несколько меньше полного припуска на обработку. Слой металла, оставшийся при этом несрезанным, образует припуск на дальнейшую обработку. Подача выбирается с учетом сечения резца, глубины резания и диаметра обрабатываемой детали. Значения подач для наиболее часто выполняемых работ на станках средней величины приведены в табл. 14, 16, 18 и 20.
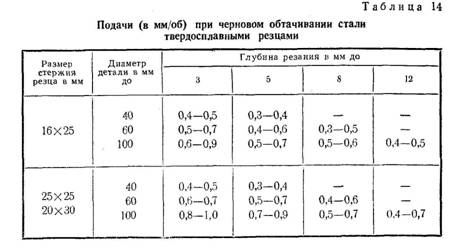
Определение скорости резания для данной обработки производится в два приема:
1) по одной из таблиц (табл. 15, 17, 19 или 21) определяется скорость резания для условий, наиболее близких к заданным;
2) числовое значение этой скорости умножается на поправочные коэффициенты, учитывающие конкретные условия предсто>ящей обработки.
Главнейшими из таких условий являются стойкость резца (коэффициент K 1 ), механические свойства обрабатываемого материала (коэффициент К 2), состояние обрабатываемой поверхности (коэффициент Кз ), материал резца (коэффициент К 4 ) и его главный угол в плане (коэффициент К 5) - Значения этих коэффициентов приведены в табл. 22.
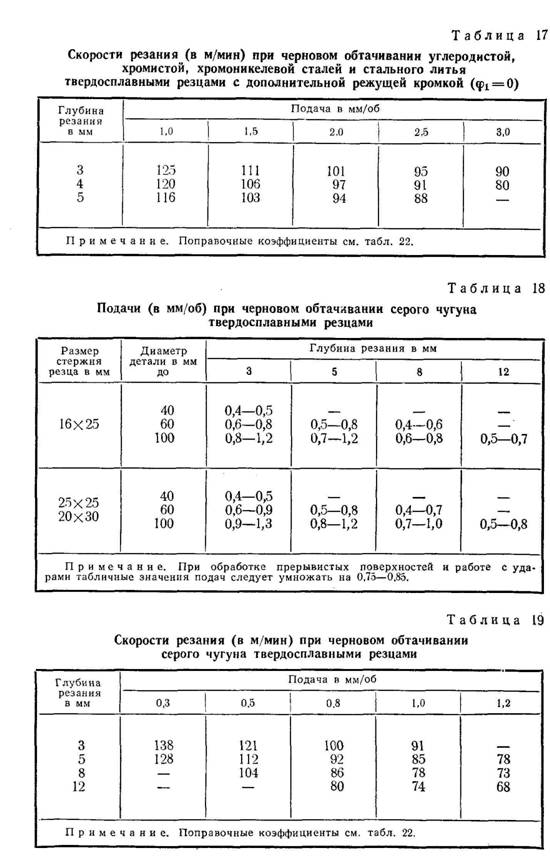
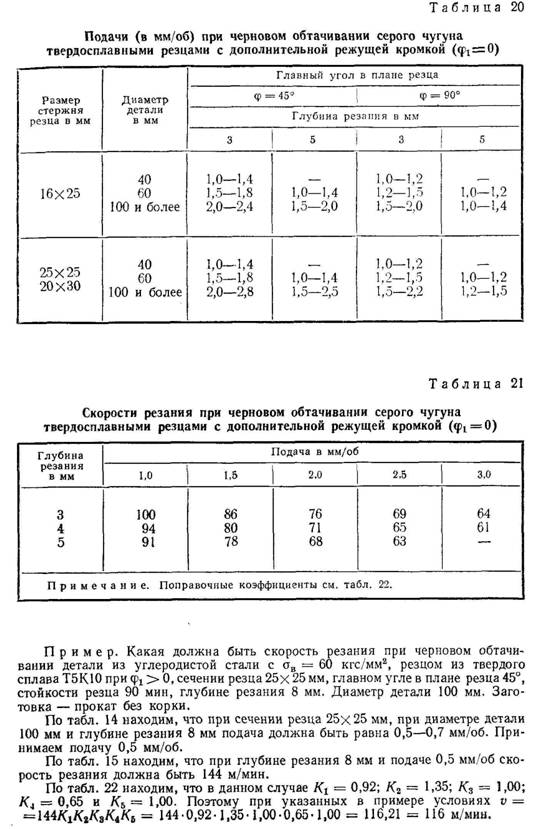
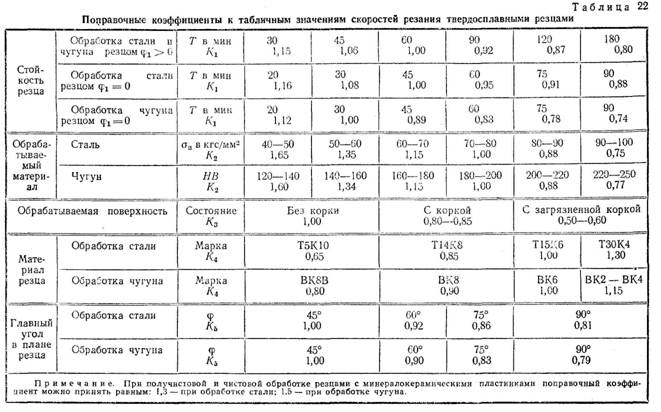
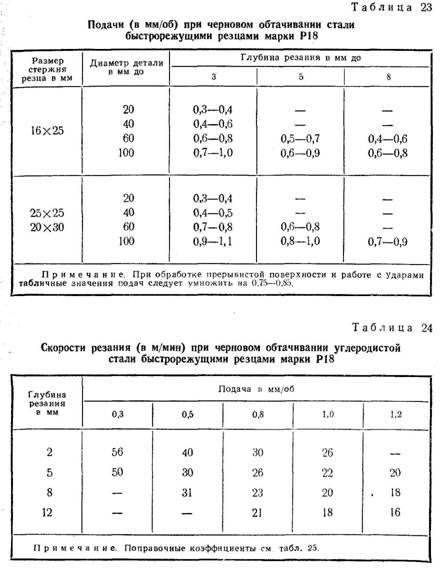
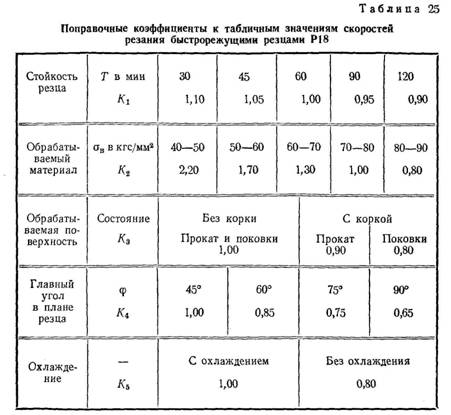
При обработке быстрорежущими резцами сталей и других материалов (кроме серого чугуна) полезно, как это указывалось выше, применять охлаждение. В качестве смазочно-охлаждающих жидкостей при обработке конструкционных и инструментальных сталей используются эмульсия и сульфофрезол, при легированных сталях — эмульсия и сурепное масло, при стальных отливках — эмульсия. При обработке серого чугуна охлаждение не применяется.
Измерения при черновом обтачивании. Грубые измерения диаметров детали при черновом обтачивании наружных цилиндрических поверхностей производятся кронциркулем и линейкой.
Простым кронциркулем (рис. 83, а ), дужки которого соединены шарниром, можно измерять диаметры до 500 мм и даже более. Пружинные кронциркули (рис. 83, б ) применяются при измерении диаметров до 50 мм, реже до 100 мм.
Пример измерения диаметра детали пружинным кронциркулем показан на рис. 84.
Раствор кронциркуля можно считать соответствующим измеряемому диаметру детали, если кронциркуль свободно проходит через нее с легким касанием и без сильного нажима. Простой кронциркуль устанавливается на требуемый размер легкими ударами наружной или внутренней стороны одной из его дужек об обрабатываемую деталь, рукоятку винта, суппорта и т. д.
Установка на требуемый раствор пружинного кронциркуля значительно удобнее, чем простого, благодаря особому устройству гайки винта, стягивающего дужки кронциркуля. Гайка (рис. 85)
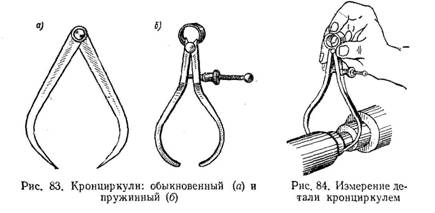
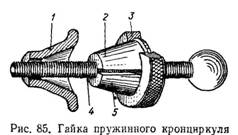
состоит из двух частей 2 и 5, соединенных (шарнирно) головкой 3. Втулочка 1 не имеет резьбы. Она свободно перемещается по винту 4 и входит в коническое гнездо, имеющееся в дужке кронциркуля. Внутренним конусом втулочка охватывает части 2 и 5 гайки и сжимает их. При вращении головки 3 раствор кронциркуля изменяется. Винт 4 имеет резьбу с мелким шагом, а поэтому установка раствора кронциркуля может быть очень точной. При необходимости значительно увеличить раствор кронциркуля достаточно сжать его дужки рукой, вследствие чего давление втулочки на части 2 и 5 гайки прекратится, и они разойдутся. Это дает возможность быстро перемещать гайку по винту, не вращая ее. Достоинство пружинного кронциркуля состоит еще в том, что раствор его не изменяется при случайных ударах дужек о деталь, части станка и т. п.
Установив раствор кронциркуля, определяют величину его по измерительной линейке (рис. 86). Такие линейки имеют миллиметровые деления. Самое маленькое деление миллиметровой шкалы линейки равно 0,5 или 1 мм.
Погрешность измерения кронциркулем и линейкой лежит в пределах от 0,3 до 0,5 мм. При установке кронциркуля на требуемый размер по точному шлифованному валику точность измерения колеблется в пределах от 0,03 до 0,05 мм, но не больше. Точность этого измерения в значительной степени зависит от состояния кронциркуля и линейки. Необходимо, чтобы рабочие поверхности губок плотно сдвинутых дужек кронциркуля соприкасались по всей длине. Вращение дужек простого кронциркуля около соединяющей их оси должно быть не слишком слабым, чтобы дужки сохраняли положение, в котором они были установлены при измерении. Если дужки кронциркуля соединены слишком туго, то при измерении детали они пружинят, а не вращаются около оси.
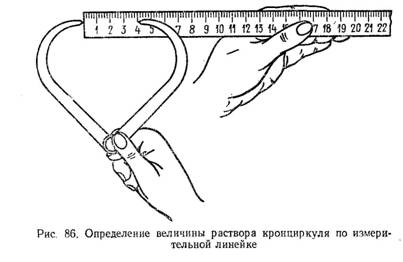
Наиболее употребительным инструментом при черновом обтачивании для измерения длин обрабатываемых деталей служит линейка с делениями. При измерении длины цилиндрических деталей необходимо, чтобы линейка соприкасалась с цилиндрической поверхностью по ее образующей (параллельно оси цилиндра). При наклонном положении линейки отсчет будет неправильным (увеличенным). При измерении диаметра линейку необходимо располагать таким образом, чтобы кромка ее проходила через центр детали, иначе будет произведено измерение не диаметра детали, а ее хорды. Отметим, что расположить линейку точно по диаметру детали очень трудно. Поэтому измерять диаметры детали линейкой следует только предварительно.
Более точные измерения диаметров обрабатываемых деталей производятся штангенциркулем с точностью отсчета до 0,1 мм.
Такой штангенциркуль типа ШЦ-1 (рис. 87) состоит из штанги 3 с губками А и С, рамки 2 с губками В и D и линейки 4, соединенной с рамкой 2. Рамка охватывает штангу 3 и может перемещаться по ней. Для закрепления рамки в требуемом положении служит винт 1 с накатной головкой.
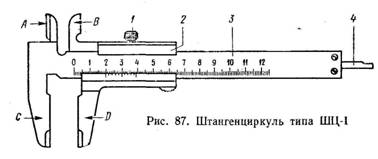
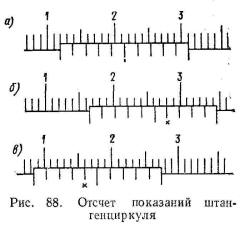
Губки С и D рассматриваемого штангенциркуля используются при измерении наружных диаметров и длины детали, губки А и В — при измерении диаметров отверстий, ширины различных канавок и т. п., а линейка 4 — для измерения длины деталей, глубины канавок, выточек и т. д. На штанге 3 нанесена шкала, каждое деление которой равно 1 мм. На нижней скошенной кромке выреза рамки '2 нанесена вторая шкала, называемая нониусом. Общая длина шкалы нониуса, разделенная на 10 частей, равна 19 делениям шкалы, нанесенной на штанге, т. е. 19 мм.
Штрихи штанги и нониуса, около которых нанесен знак нуль, называются нулевыми. Шкалы на штанге и нониусе расположены таким образом, что когда губки штангенциркуля сдвинуты плотно, нулевой штрих нониуса точно совпадает с нулевым штрихом штанги. Поэтому измерение длин, диаметров и т. д., содержащих целое число миллиметров, производится по нулевому штриху нониуса. Если, например, при измерении какой-либо детали нулевой штрих нониуса точно совпал с 12-м штрихом штанги (рис. 88, а), это значит, что данный размер детали равен 12 мм. Если нулевой штрих нониуса не совпадает с каким-либо штрихом штанги, замечают прежде всего, какой штрих штанги уже пройден нулевым штрихом нониуса. На рис. 88, б это 16-й штрих. Затем смотрят, какой штрих нониуса лучше всех остальных совпадает с каким-либо штрихом штанги. На рисунке это 6-й штрих. Это значит, что штангенциркуль установлен на размер 16,6 мм. Показание штангенциркуля на рис. 88, в соответствует размеру 8,4 мм. Таким образом, величина отсчета по нониусу рассмотренного штангенциркуля составляет 0,1 мм. Погрешность измерения лежит в пределах ±0,1 мм и зависит от точности отсчета по нониусу и от измеряемой длины.
Измерение небольшого наружного диаметра детали штангенциркулем показано на рис. 89, а. При таком измерении штанга штангенциркуля не должна касаться поверхности измеряемой детали. Если штангенциркуль окажется в положении, показанном на рис. 89, б, то будет измерена, очевидно, хорда, а не диаметр детали. Правильный способ применения штангенциркуля для измерения большого наружного диаметра детали изображен на рис. 89, в. Если при плотно сдвинутых губках штангенциркуля нулевой штрих нониуса не совпадает с нулевым штрихом штанги, или при совпадении этих штрихов рабочие поверхности губок касаются друг друга не по всей своей длине, это означает, что штангенциркуль неисправен и должен быть сдан в ремонт.
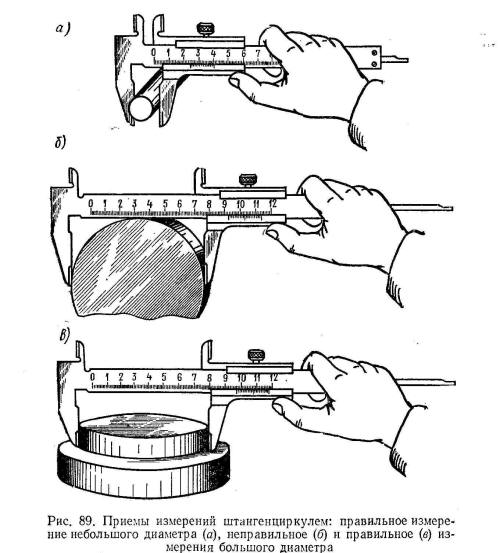
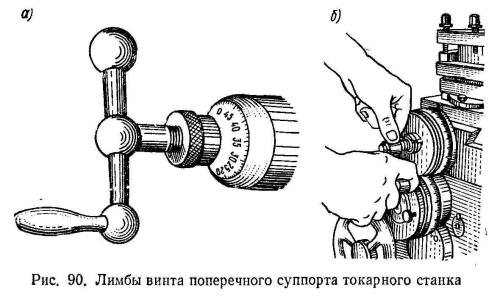
Отметим, что иногда значительное уменьшение времени, затрачиваемого на измерение детали, достигается путем использования лимбов винтов суппорта. Одно деление лимба, показанного на рис. 90, а, соответствует изменению диаметра обрабатываемой детали на 0,1 мм.
Если, например, после прохода резца диаметр детали получился равным 40,6 мм, причем с неподвижной риской совпало 26-е деление рассматриваемого лимба, а перед следующим проходом резца рукоятка повернута так, чтобы с неподвижной риской совпало 28-е деление лимба, то диаметр детали получится равным 40,6 — 0,2 = 40,4 мм.
Существуют лимбы, обеспечивающие более точный отсчет перемещения резца, а следовательно, и получение более точного диаметра обрабатываемой поверхности детали, как например, лимб, установка по которому резца показана на рис. 90, б.
Точность размеров деталей и шероховатость поверхностей, получающихся при черновом обтачивании. Диаметры детали при черновом обтачивании получаются в пределах 4—5-го классов точности, а шероховатость обработанных поверхностей в пределах 3—4-го классов чистоты.
Другие статьи по теме:
Комментарии и вопросы:
Комментариев пока нет, но ваш может быть первым.Разметить комментарий или вопрос